
- #Programming with robotc how to#
- #Programming with robotc update#
- #Programming with robotc driver#
- #Programming with robotc manual#
- #Programming with robotc archive#
Proceed to the next step if there are no errors.
#Programming with robotc archive#
(This is in the folder you unzipped the downloaded archive to). Getting started: Balancing for the first time:īefore moving on to more advanced programs, we’ll first configure and run a simple program that will make the Segway balance and just stay in the same place.
#Programming with robotc driver#
#Programming with robotc update#
#Programming with robotc how to#
The next article in our series will examine lights out manufacturing and whether it makes sense for your business.This tutorial will show you how to use and modify RobotC program code to create a working LEGO NXT Segway that you can customize as you like. This method is popular for programming cobots. And as with the teach pendant, the operator stores each position in the robot computer. Because this method uses the physical robot for programming, there is downtime associated with it, yet the ease of programming enhances overall productivity. Lead through programming is a method of programming robots through demonstration in which the operator physically moves the robot through the desired task either by manipulation of a force sensor or a joystick attached to the robot wrist above the end effector. Because it allows the operator to simply move the robot to the desired position, it is intuitive and easy to learn and faster than other programming methods. Teaching by Demonstration or Lead Through Once a technician is satisfied with the program, it can then be downloaded to the robot.
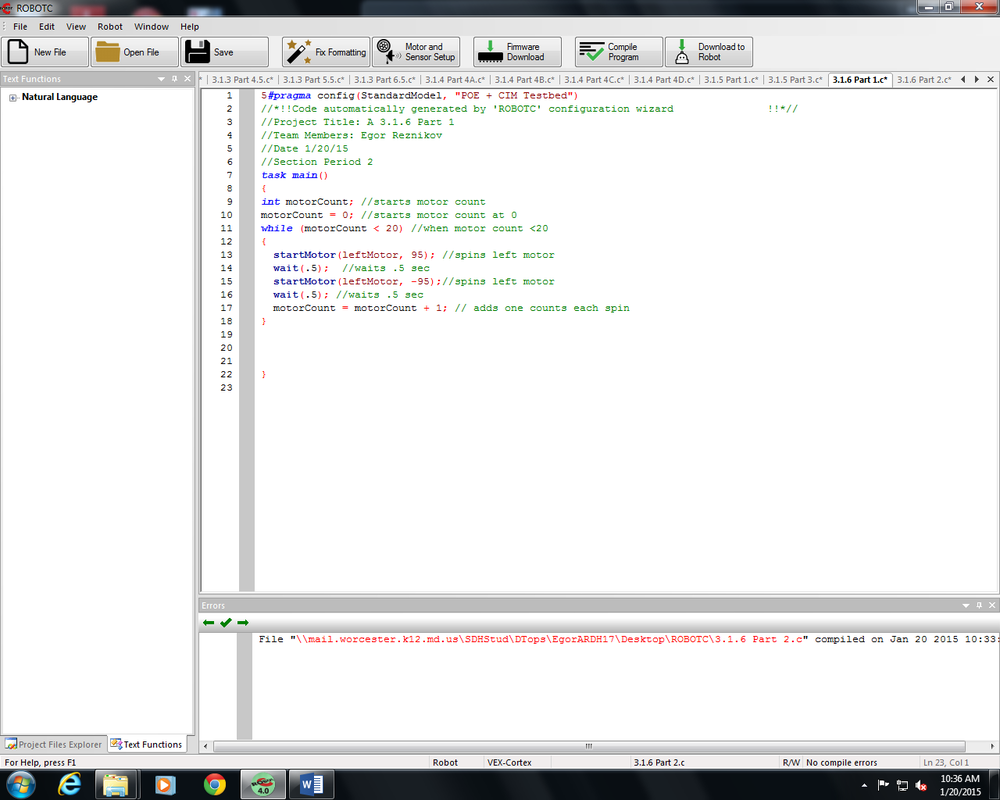
#Programming with robotc manual#
OLP is often used in robotic research and is well suited to complex applications that would require extensive time for manual programming such as in manufacturing production with high part mixes but low volumes. Adjustments and reconfigurations can be made to the application simulation before running the program live, ensuring programming accuracy.

OLP is ideal for testing different approaches to a problem, which would be highly inefficient for online programming methods. This enables quicker deployment and minimal loss of productivity.
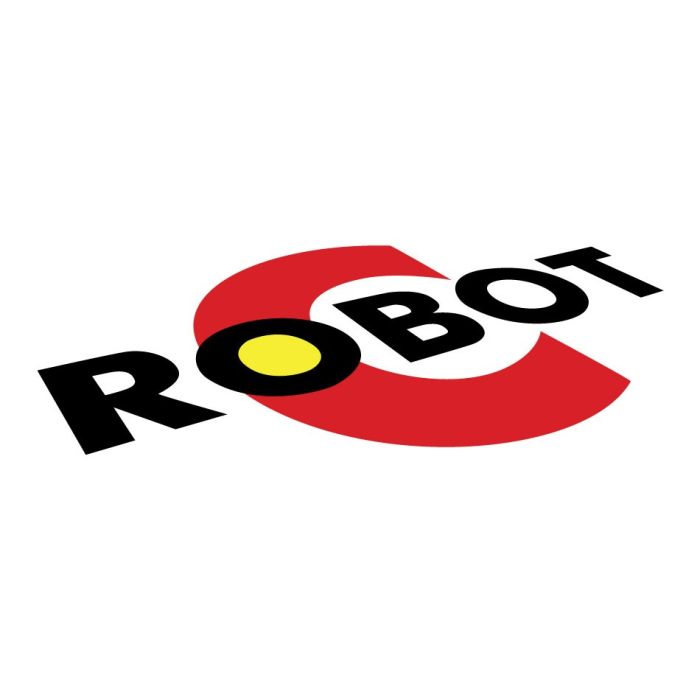
Offline programming (OLP), or simulation, is an advancement in programming because programs are developed offline, and the robot only needs to stop operations while the new program is being downloaded and tested. It is therefore disruptive to the manufacturing process and results in some lost productivity. Teach pendants make it easy to make robots operational without needing to purchase or integrate additional programming software. However, there is one major downside to this programming method and that is that robot operations must be stopped while it is being programmed. The most common method of programming robots is through a handheld teach pendant device, today usually a touch screen tablet, on which an operator inputs commands to the robot. Most industrial robots come with a teach pendant, and it is therefore the most familiar programming method to technicians. The key characteristic of this programming method is the way the robot is taught positional data, and it allows precise positioning. The teach pendant is used to manually drive the robot to its desired location, and locations are then stored and can be revisited within the robot program. The most common programming methods for industry robots are teach pendants, offline programming or simulation, and lead through demonstration. Each programming method has specific advantages and disadvantages depending on operator needs. Programming is key to any robotic system because it is how information and instructions are communicated to the robot to make it function and carry out tasks.
